Audience | Membres et mentors d’équipe en Défi techno FIRST * et Compétition de robotique FIRST |
Objectif(s) | Développer un design et concevoir un robot ou un mécanisme en prenant en considération les principes de physique et d’ingénierie – Matériaux et structures – Plateforme pilotable – groupe motopropulseur – Motorisation – Pneumatique – Systèmes de transmission |
Type de contenu | Informatif |
Format de contenu | Texte, vidéos YouTube |
Cours préalable | Aucun |
Prérequis | Aucun |
Matériel | |
Niveau | Débutant à intermédiaire |
Compétences requises | Volonté d’apprendre Travail avec des outils à main et électrique |
Auteur(s) | Adaptation par Martin Regimbald |
Historique | 3 septembre 2024 – Publication sur Campus |
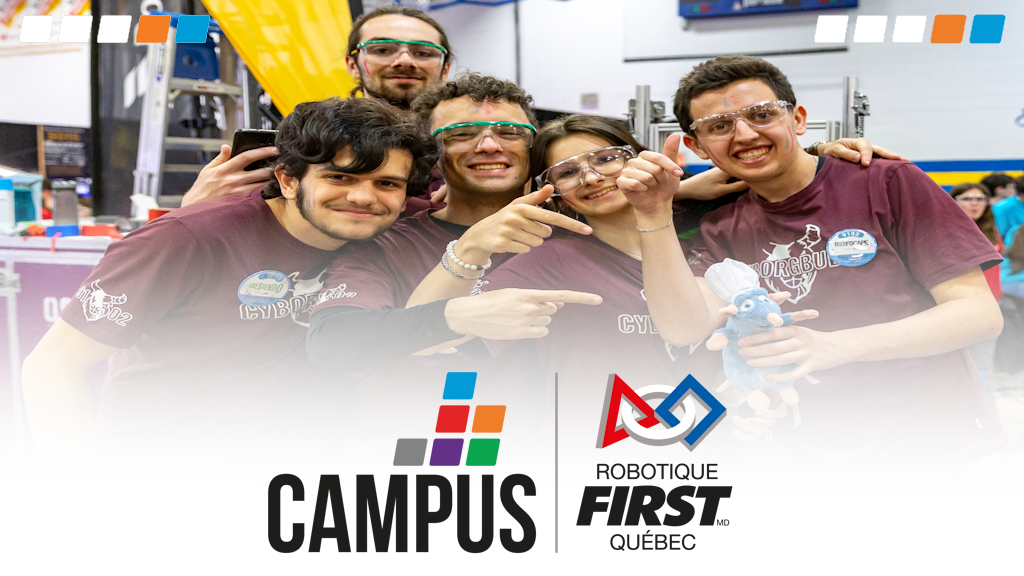